Effect of Exploitation Conditions and Flaw Geometry on the Load Carrying Capacity of Casing Pipes for Oil Drilling Rigs
Само за регистроване кориснике
2014
Конференцијски прилог (Објављена верзија)
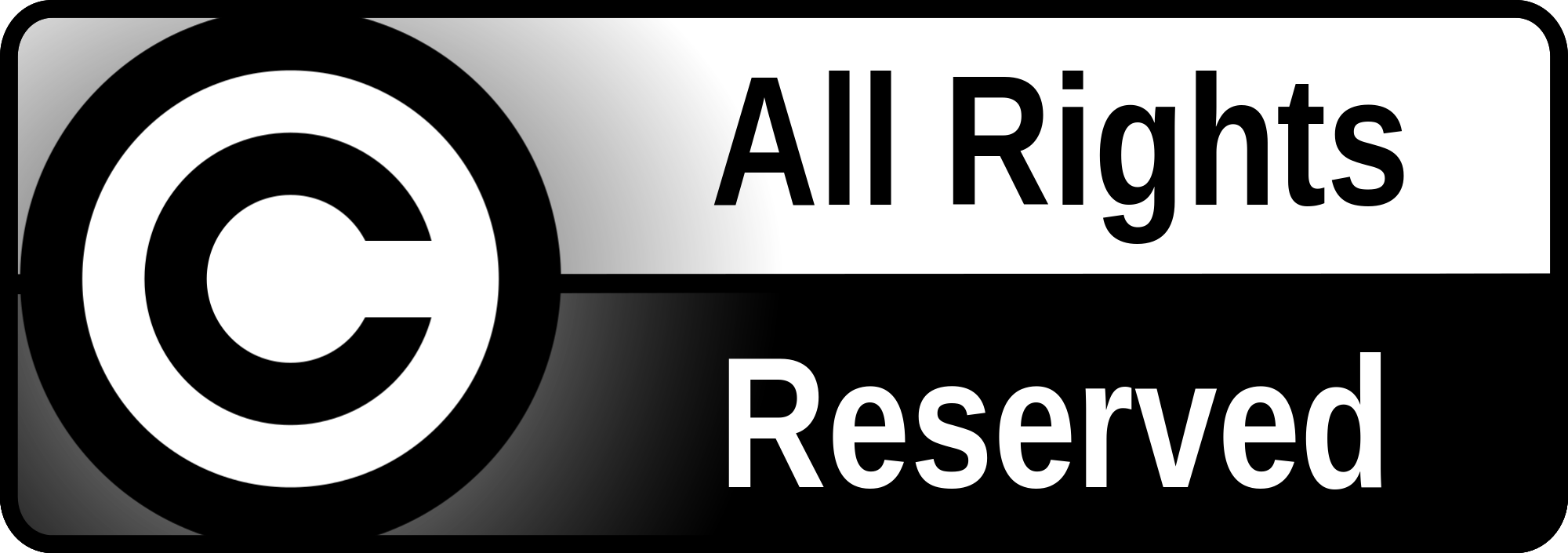
Метаподаци
Приказ свих података о документуАпстракт
The subject of this work is examination of API J55 steel casing pipes manufactured by high frequency (HF) contact welding. Since the pipes were withdrawn after about 70 000 hours of service in an oil drilling rig, the influence of the exploitation conditions on the material properties is determined. Experimental analysis includes tensile, impact toughness and fatigue testing of the specimens cut from the exploited pipe and the new pipe manufactured from the same-grade material. Additionally, pipe with flaws (stress concentrators) is tested by subjecting to internal pressure. The analysed stress concentrators represent defects which are often found in the exploitation: localized corrosion damages (corrosion pits). They were simulated by machining on the external surface of the pipe wall. The behavior of the pipes with these defects is determined by strain measurement and finite element analysis in software package Abaqus. The dimensions of the defects are varied, in order to determine t...he dependence of load carrying capacity on their depth and length. Several expressions from the literature are applied for estimation of the maximum pressure in damaged pipelines, and the solutions are compared with the predictions of finite element models. Additionally, triaxiality values at the bottom of the defects are compared with those obtained on tensile specimens, having in mind the key role of this parameter in ductile fracture initiation.
Кључне речи:
Casing pipes / Properties degradation / Integrity assessment / Stress concentrator / Finite element methodИзвор:
Proceedings of the 14th Symposium on Experimental Stress Analysis and Materials Testing, 2014, 601, 65-+Издавач:
- Trans Tech Publications Ltd, Durnten-Zurich
Финансирање / пројекти:
- Микромеханички критеријуми оштећења и лома (RS-MESTD-Basic Research (BR or ON)-174004)
- Развој нових методологија ревитализације турбинске и хидромеханичке опреме хидроелектрана у зависности од узрока деградације материјала (RS-MESTD-Technological Development (TD or TR)-35002)
DOI: 10.4028/www.scientific.net/KEM.601.65
ISBN: 978-303835048-4
ISSN: 1013-9826
WoS: 000343792400015
Scopus: 2-s2.0-84898958610
Институција/група
Tehnološko-metalurški fakultetTY - CONF AU - Rakin, Marko AU - Međo, Bojan AU - Arsić, Miodrag AU - Šarkočević, Živče AU - Sedmak, Aleksandar PY - 2014 UR - http://TechnoRep.tmf.bg.ac.rs/handle/123456789/2740 AB - The subject of this work is examination of API J55 steel casing pipes manufactured by high frequency (HF) contact welding. Since the pipes were withdrawn after about 70 000 hours of service in an oil drilling rig, the influence of the exploitation conditions on the material properties is determined. Experimental analysis includes tensile, impact toughness and fatigue testing of the specimens cut from the exploited pipe and the new pipe manufactured from the same-grade material. Additionally, pipe with flaws (stress concentrators) is tested by subjecting to internal pressure. The analysed stress concentrators represent defects which are often found in the exploitation: localized corrosion damages (corrosion pits). They were simulated by machining on the external surface of the pipe wall. The behavior of the pipes with these defects is determined by strain measurement and finite element analysis in software package Abaqus. The dimensions of the defects are varied, in order to determine the dependence of load carrying capacity on their depth and length. Several expressions from the literature are applied for estimation of the maximum pressure in damaged pipelines, and the solutions are compared with the predictions of finite element models. Additionally, triaxiality values at the bottom of the defects are compared with those obtained on tensile specimens, having in mind the key role of this parameter in ductile fracture initiation. PB - Trans Tech Publications Ltd, Durnten-Zurich C3 - Proceedings of the 14th Symposium on Experimental Stress Analysis and Materials Testing T1 - Effect of Exploitation Conditions and Flaw Geometry on the Load Carrying Capacity of Casing Pipes for Oil Drilling Rigs EP - + SP - 65 VL - 601 DO - 10.4028/www.scientific.net/KEM.601.65 ER -
@conference{ author = "Rakin, Marko and Međo, Bojan and Arsić, Miodrag and Šarkočević, Živče and Sedmak, Aleksandar", year = "2014", abstract = "The subject of this work is examination of API J55 steel casing pipes manufactured by high frequency (HF) contact welding. Since the pipes were withdrawn after about 70 000 hours of service in an oil drilling rig, the influence of the exploitation conditions on the material properties is determined. Experimental analysis includes tensile, impact toughness and fatigue testing of the specimens cut from the exploited pipe and the new pipe manufactured from the same-grade material. Additionally, pipe with flaws (stress concentrators) is tested by subjecting to internal pressure. The analysed stress concentrators represent defects which are often found in the exploitation: localized corrosion damages (corrosion pits). They were simulated by machining on the external surface of the pipe wall. The behavior of the pipes with these defects is determined by strain measurement and finite element analysis in software package Abaqus. The dimensions of the defects are varied, in order to determine the dependence of load carrying capacity on their depth and length. Several expressions from the literature are applied for estimation of the maximum pressure in damaged pipelines, and the solutions are compared with the predictions of finite element models. Additionally, triaxiality values at the bottom of the defects are compared with those obtained on tensile specimens, having in mind the key role of this parameter in ductile fracture initiation.", publisher = "Trans Tech Publications Ltd, Durnten-Zurich", journal = "Proceedings of the 14th Symposium on Experimental Stress Analysis and Materials Testing", title = "Effect of Exploitation Conditions and Flaw Geometry on the Load Carrying Capacity of Casing Pipes for Oil Drilling Rigs", pages = "+-65", volume = "601", doi = "10.4028/www.scientific.net/KEM.601.65" }
Rakin, M., Međo, B., Arsić, M., Šarkočević, Ž.,& Sedmak, A.. (2014). Effect of Exploitation Conditions and Flaw Geometry on the Load Carrying Capacity of Casing Pipes for Oil Drilling Rigs. in Proceedings of the 14th Symposium on Experimental Stress Analysis and Materials Testing Trans Tech Publications Ltd, Durnten-Zurich., 601, 65-+. https://doi.org/10.4028/www.scientific.net/KEM.601.65
Rakin M, Međo B, Arsić M, Šarkočević Ž, Sedmak A. Effect of Exploitation Conditions and Flaw Geometry on the Load Carrying Capacity of Casing Pipes for Oil Drilling Rigs. in Proceedings of the 14th Symposium on Experimental Stress Analysis and Materials Testing. 2014;601:65-+. doi:10.4028/www.scientific.net/KEM.601.65 .
Rakin, Marko, Međo, Bojan, Arsić, Miodrag, Šarkočević, Živče, Sedmak, Aleksandar, "Effect of Exploitation Conditions and Flaw Geometry on the Load Carrying Capacity of Casing Pipes for Oil Drilling Rigs" in Proceedings of the 14th Symposium on Experimental Stress Analysis and Materials Testing, 601 (2014):65-+, https://doi.org/10.4028/www.scientific.net/KEM.601.65 . .