Response Surface Methodology and Artificial Neural Network-Based Models for Predicting Roughness of Cu coatings
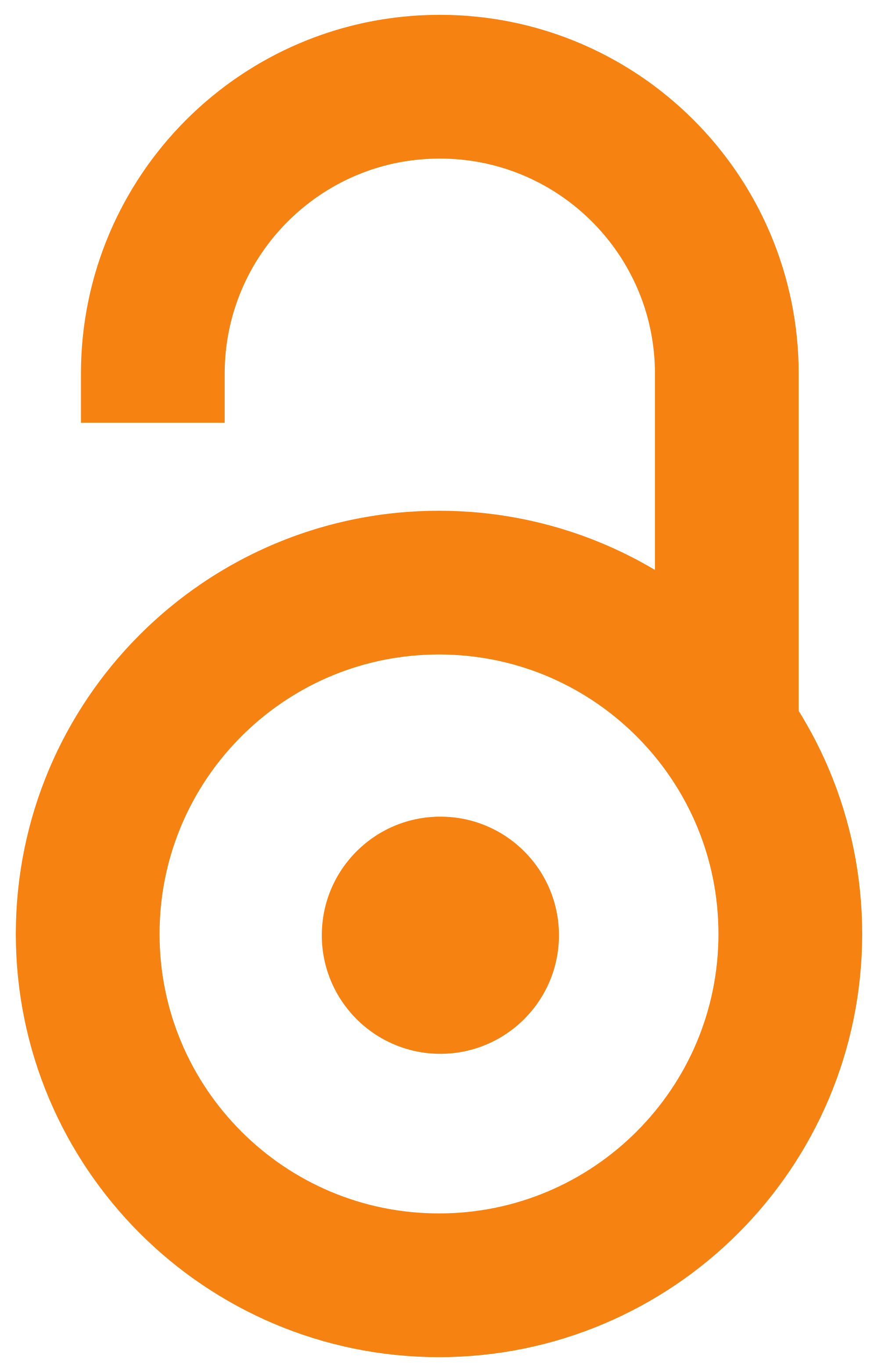
2020
Аутори
Mladenović, Ivana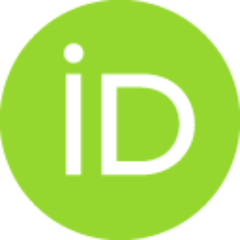
Lamovec, Jelena
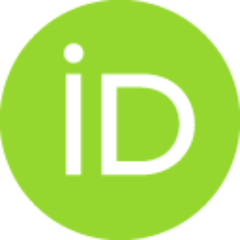
Nikolić, Nebojša
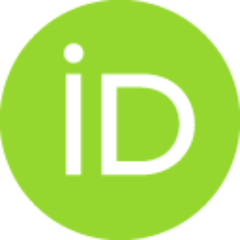
Andrić, Stevan
Obradov, Marko
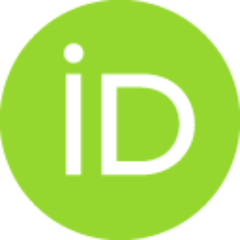
Radojević, Vesna
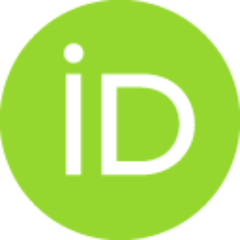
Vasiljević-Radović, Dana
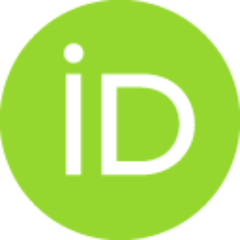
Конференцијски прилог (Објављена верзија)
Метаподаци
Приказ свих података о документуАпстракт
Copper coatings are produced on silicon wafer by electrodeposition (ED) in pulsating current (PC) regime. Electrodeposition was performed at various current density amplitudes in the range of 80−140 mA cm-2, frequency in the range of 30−100 Hz and coating thickness in the range of 10−60 μm. The resulting composite systems consist of monolayered copper films electrodeposited from sulfate bath on Si wafers with sputtered layers of Cr/Au. Roughness measurements were performed to evaluate properties of the copper coating surface. The coating roughness (R) was measured using Atomic Force Microscope in contact mode. The software Gwyddion was used for determination an average roughness parameter (Ra). After that (Artificial Neural Network-ANN) model was used to study the relationship between the parameters of electrodeposition process and roughness of copper coatings. The influence of experimental values: amplitude current density, frequency and thickness of coating on the surface roughness w...ill be highlighted. Response surface methodology (RSM) was utilized to improve the correction between Ra and input parameters. Finally, the results of the average roughness (experimental and predicted) were used to estimate the new value of (Ra) of copper for each variation of the input parameters and compared capability of ANN and regression analysis for surface roughness generated under different electrochemical conditions. The coefficient of determination was found 92% for ANN and 93% for regression analysis.
Кључне речи:
electrodeposition / electrodeposition / roughness / AFM / coatings / ANN / RSM / Artificial Neural Network / models / prediction / roughness / AFM / coatings / ANN / RSM.Извор:
Proceedings - 7th International Conference on Electrical, Electronic and Computing Engineering IcETR, 2020Издавач:
- Belgrade: ETRAN – Society for electronics, telecommunication, computing, automatics and nuclear angineering
Финансирање / пројекти:
- Министарство науке, технолошког развоја и иновација Републике Србије, институционално финансирање - 200026 (Универзитет у Београду, Институт за хемију, технологију и металургију - ИХТМ) (RS-MESTD-inst-2020-200026)
- Министарство науке, технолошког развоја и иновација Републике Србије, институционално финансирање - 200135 (Универзитет у Београду, Технолошко-металуршки факултет) (RS-MESTD-inst-2020-200135)
Институција/група
Tehnološko-metalurški fakultetTY - CONF AU - Mladenović, Ivana AU - Lamovec, Jelena AU - Nikolić, Nebojša AU - Andrić, Stevan AU - Obradov, Marko AU - Radojević, Vesna AU - Vasiljević-Radović, Dana PY - 2020 UR - http://TechnoRep.tmf.bg.ac.rs/handle/123456789/4420 AB - Copper coatings are produced on silicon wafer by electrodeposition (ED) in pulsating current (PC) regime. Electrodeposition was performed at various current density amplitudes in the range of 80−140 mA cm-2, frequency in the range of 30−100 Hz and coating thickness in the range of 10−60 μm. The resulting composite systems consist of monolayered copper films electrodeposited from sulfate bath on Si wafers with sputtered layers of Cr/Au. Roughness measurements were performed to evaluate properties of the copper coating surface. The coating roughness (R) was measured using Atomic Force Microscope in contact mode. The software Gwyddion was used for determination an average roughness parameter (Ra). After that (Artificial Neural Network-ANN) model was used to study the relationship between the parameters of electrodeposition process and roughness of copper coatings. The influence of experimental values: amplitude current density, frequency and thickness of coating on the surface roughness will be highlighted. Response surface methodology (RSM) was utilized to improve the correction between Ra and input parameters. Finally, the results of the average roughness (experimental and predicted) were used to estimate the new value of (Ra) of copper for each variation of the input parameters and compared capability of ANN and regression analysis for surface roughness generated under different electrochemical conditions. The coefficient of determination was found 92% for ANN and 93% for regression analysis. PB - Belgrade: ETRAN – Society for electronics, telecommunication, computing, automatics and nuclear angineering C3 - Proceedings - 7th International Conference on Electrical, Electronic and Computing Engineering IcETR T1 - Response Surface Methodology and Artificial Neural Network-Based Models for Predicting Roughness of Cu coatings UR - https://hdl.handle.net/21.15107/rcub_technorep_4420 ER -
@conference{ author = "Mladenović, Ivana and Lamovec, Jelena and Nikolić, Nebojša and Andrić, Stevan and Obradov, Marko and Radojević, Vesna and Vasiljević-Radović, Dana", year = "2020", abstract = "Copper coatings are produced on silicon wafer by electrodeposition (ED) in pulsating current (PC) regime. Electrodeposition was performed at various current density amplitudes in the range of 80−140 mA cm-2, frequency in the range of 30−100 Hz and coating thickness in the range of 10−60 μm. The resulting composite systems consist of monolayered copper films electrodeposited from sulfate bath on Si wafers with sputtered layers of Cr/Au. Roughness measurements were performed to evaluate properties of the copper coating surface. The coating roughness (R) was measured using Atomic Force Microscope in contact mode. The software Gwyddion was used for determination an average roughness parameter (Ra). After that (Artificial Neural Network-ANN) model was used to study the relationship between the parameters of electrodeposition process and roughness of copper coatings. The influence of experimental values: amplitude current density, frequency and thickness of coating on the surface roughness will be highlighted. Response surface methodology (RSM) was utilized to improve the correction between Ra and input parameters. Finally, the results of the average roughness (experimental and predicted) were used to estimate the new value of (Ra) of copper for each variation of the input parameters and compared capability of ANN and regression analysis for surface roughness generated under different electrochemical conditions. The coefficient of determination was found 92% for ANN and 93% for regression analysis.", publisher = "Belgrade: ETRAN – Society for electronics, telecommunication, computing, automatics and nuclear angineering", journal = "Proceedings - 7th International Conference on Electrical, Electronic and Computing Engineering IcETR", title = "Response Surface Methodology and Artificial Neural Network-Based Models for Predicting Roughness of Cu coatings", url = "https://hdl.handle.net/21.15107/rcub_technorep_4420" }
Mladenović, I., Lamovec, J., Nikolić, N., Andrić, S., Obradov, M., Radojević, V.,& Vasiljević-Radović, D.. (2020). Response Surface Methodology and Artificial Neural Network-Based Models for Predicting Roughness of Cu coatings. in Proceedings - 7th International Conference on Electrical, Electronic and Computing Engineering IcETR Belgrade: ETRAN – Society for electronics, telecommunication, computing, automatics and nuclear angineering.. https://hdl.handle.net/21.15107/rcub_technorep_4420
Mladenović I, Lamovec J, Nikolić N, Andrić S, Obradov M, Radojević V, Vasiljević-Radović D. Response Surface Methodology and Artificial Neural Network-Based Models for Predicting Roughness of Cu coatings. in Proceedings - 7th International Conference on Electrical, Electronic and Computing Engineering IcETR. 2020;. https://hdl.handle.net/21.15107/rcub_technorep_4420 .
Mladenović, Ivana, Lamovec, Jelena, Nikolić, Nebojša, Andrić, Stevan, Obradov, Marko, Radojević, Vesna, Vasiljević-Radović, Dana, "Response Surface Methodology and Artificial Neural Network-Based Models for Predicting Roughness of Cu coatings" in Proceedings - 7th International Conference on Electrical, Electronic and Computing Engineering IcETR (2020), https://hdl.handle.net/21.15107/rcub_technorep_4420 .